Research indicates that from an energy perspective, helium is the most sustainable method of gas atomization for metallic powder production and that the specific energy consumption critically depends on process parameters and alloy chemistry. Mechanical powder production such as ball milling, when appropriate for additive manufacturing, requires significantly less energy than atomization.
HOLLYWOOD, Fla. — (BUSINESS WIRE) — April 16, 2024 — The Additive Manufacturer Green Trade Association (“AMGTA”) a global advocacy group focused on promoting sustainable additive manufacturing (“AM”) industry practices, announced today the preliminary results of a research project titled “Specific Energy of Metal AM Feedstock: A Comparison.” The study, commissioned by the AMGTA and conducted by Syntec Associates, a research consultancy, in partnership with Divergent Technologies, a complete modular digital factory for complex structures, evaluated three key metal AM feedstock processing approaches—gas atomization, mechanical milling (specifically ball milling), and wire drawing—to determine specific energy requirements for producing feedstock materials. The research findings highlighted that, from an energy perspective, helium gas atomization is the most sustainable method used for gas atomization for metallic powder production of commonly used alloys, followed by argon and then nitrogen. Specific energy consumption for atomization also critically depends on process parameters and alloy chemistry. Additionally, research showed that mechanical milling, when appropriate for use in powder production in additive manufacturing, exhibits a significant reduction in specific energy consumption when compared to gas atomization.
This press release features multimedia. View the full release here: https://www.businesswire.com/news/home/20240416215703/en/
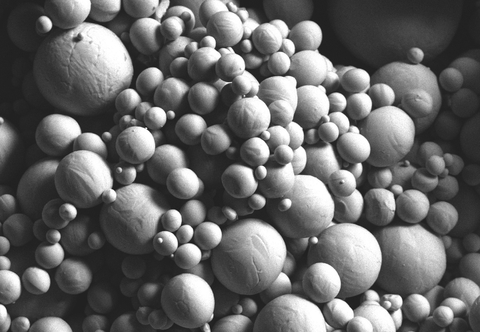
Photo courtesy of Carpenter Additive
“When preparing life cycle assessments on industrial rate processing of our alloys, I found wide variation in the literature on AM process and powder atomization energy consumption,” said Michael Kenworthy, Chief Technology Officer at Divergent Technologies and AMGTA Board Director. “This research established a transparent set of process assumptions and models from which to understand the key process levers and evaluate system trade studies that inform future sustainability enhancements.”
Key takeaways from this study include:
- Helium Gas Atomization is Best for Powder Atomization: Research indicates that, from an energy perspective, helium gas atomization stands out as the most sustainable gas atomization method, showing a significant reduction in specific energy consumption compared to argon and nitrogen for commonly used alloys.
- Argon Atomized Powder is Better than Nitrogen: For those seeking an alternative to helium, argon-atomized powder is revealed to be a notable option, energy savings when compared to nitrogen-atomized powder.
- Mechanical Milling Outperforms Gas Atomization: Mechanical milling, particularly ball milling, demonstrates a significant reduction in specific energy consumption compared to gas atomization for metal AM powder production.
- Industry Guidance for Sustainable Choices: This research highlights the importance of selecting manufacturing methods with the lowest specific energy consumption per kilogram to enhance overall sustainability when producing feedstock materials used in additive manufacturing.
“A primary goal of the AMGTA is to educate the consumer on the most sustainable methods of production within the additive supply chain. This important piece of research provides guidance on which methods of gas atomization require the least amount of specific energy per kilogram,” said Brian R. Neff, AMGTA’s Board Chair. “At the same time, it indicates to the market that mechanical production methods of powder feedstock, such as ball milling, are themselves an order of magnitude better than gas atomization from an energy perspective.”
Gas atomization, deemed a promising technology for producing stock powders for additive manufacturing, was a focal point of the study. The research revealed that gas atomization using helium as the atomization gas resulted in the least total specific energy consumption compared to argon (13% better on average) and nitrogen (28% better on average). Additionally, argon-atomized powder was found to reduce energy requirements by 12% when compared to nitrogen-atomized powder for the alloys studied (SS316L, Al5083, and IN718).
The study also highlights the efficiency of mechanical powder production, particularly ball milling, which showed approximately a 90% improvement in specific energy consumption compared to gas atomization for the range of process conditions studied. Further research is recommended to determine the applied impact within specific product categories of using helium-atomized powder and/or ball milled powder.
“This research aligns with the AMGTA commitment to better understand sustainable manufacturing practices leveraging additive technologies,” said Sherri Monroe, the AMGTA’s Executive Director. “These findings highlight key considerations for manufacturers seeking environmentally friendly feedstock production methods. To advance sustainability in additive manufacturing, research is vital in order to make informed decisions.”
Highlights from the study can be found on the AMGTA’s website. The AMGTA says it expects to publish additional independent research throughout 2024. Additional information on this study and others conducted by the AMGTA can be found on the AMGTA website, www.AMGTA.org.
About the AMGTA
The AMGTA was launched in 2019 to better understand and promote the environmental benefits of additive manufacturing across the global economy. AMGTA members represent the entirety of the manufacturing spectrum - from design and raw materials to end products and users - focused on innovating better, more sustainable, and financially advantageous products through best additive practices. For more information, please visit www.amgta.org.
View source version on businesswire.com: https://www.businesswire.com/news/home/20240416215703/en/
Contact:
Sherri Monroe
smonroe@amgta.org
954.308.0888