Deliver Better-than 0.1% Precision Performance in Temperature, Pressure, and Other Measurements, Ideal for Both Manufacturing and Test and Measurement Equipment
TOKYO — (BUSINESS WIRE) — May 28, 2019 — Renesas Electronics Corporation (TSE: 6723), a premier supplier of advanced semiconductor solutions, today introduced the RX23E-A Group 32-bit RX microcontrollers (MCUs), combining high-precision analog front end (AFE) and an MCU on a single chip. Designed for manufacturing and test and measurement equipment applications that require high-precision measurements of analog signals for temperature, pressure, weight, and flow, the RX23E-A MCUs are the first Renesas solutions to enable such signals to be measured with better than 0.1% precision without calibration.
This press release features multimedia. View the full release here: https://www.businesswire.com/news/home/20190528005204/en/
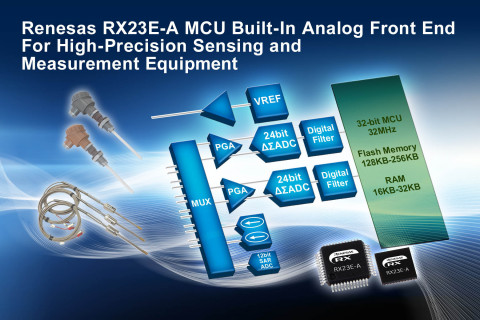
Renesas RX23E-A MCU built-in analog front end for high-precision sensing and measurement equipment (Graphic: Business Wire)
The new MCUs achieve AFE precision at the highest class in the industry (offset drift: 10 nV/°C, gain drift: 1 ppm/°C, and RMS noise: 30 nV rms), a level that could previously only be achieved by combining dedicated A/D converter circuits with high-precision operational amplifier ICs. By integrating this high-precision AFE IP (intellectual property) on a single chip using the same fabrication process technology, Renesas has made it possible to implement high-precision sensor measurement, computation, control, and communications on a single chip. This allows system manufactures to reduce the number of required components, save space, and simplify system design in a wide range of equipment requiring high-precision measurement, such as sensing, temperature controllers, recording, weighing, and force sensing. It also accelerates endpoint intelligence by enabling distributed processing with MCUs.
“The RX23E-A MCUs will radically evolve the structure of high-precision analog measurement systems,” said Akira Denda, Vice President, Industrial Automation Business Division, Renesas Electronics Corporation. “Moving forward, Renesas is aiming to deliver an extensive product line, starting with the RX23E-A Group, that integrates MCUs and high-precision analog on a single chip for programmable logic controllers, distributed control system applications, and test and measurement equipment that require a variety of higher precision measurements.”
With big data-driven quality and productivity improvements, the pressure is on for factories and manufacturing sites to measure a wide variety of sensor data accurately and reliably. Since users require stability when measuring small signals at high precision over a wide environmental temperature range, it is important to reduce noise characteristics and temperature drift characteristics to low levels. To address these needs, Renesas has developed a high-precision AFE and integrated it into an RX MCU with an extensive track record with industrial applications.
The RX23E-A MCUs are based on the RXv2 core, which features operating speeds of 32 MHz, a digital signal processor (DSP), and superlative floating point unit (FPU) calculations. This allows the implementation of adaptive control using temperature data and inverse matrix calculations using 6-axis distortion data. For example, robot arm force sensors require the measurement and calculation of the 6-axis distortion in a small space. The RX23E-A MCUs make it possible to measure the 6-axis distortion data and perform the inverse matrix calculations with a single chip.
Key features of the RX23E-A MCUs
-
AFE block
- 24-bit delta-sigma A/D converter: Up to 23 bits of effective resolution. Data output rate flexible at 7.6 PS to 15.6 kPS.
- Two 24-bit delta-sigma A/D converters that can start synchronously, allowing sensor temperature correction to be performed without switching channels.
- PGA (programmable gain amplifier): Rail-to-rail input PGA allows amplification up to 128×. Offset drift: 10 nV/°C, gain drift: 1 ppm/°C, and RMS noise: 30 nV rms.
- Voltage reference: Low temperature drift characteristics of 4 ppm/°C with superlative temperature stabilization.
- Excitation current source: Programmable current source with required matching required for 3-wire resistance temperature detector.
- Analog inputs: differential inputs: up to 6 channels, pseudo-differential inputs: up to 11 channels, single-ended inputs: up to 11 channels. All can be used as inputs to the two A/D converters.
-
MCU block
- CPU: 32-bit RXv2 core operating at 32 MHz
- Digital signal processing can be implemented with DPS instructions and FPU.
- ROM/RAM: ROM: 128 to 256 KB, RAM: 16 to 32 KB.
- Communication interfaces: SPI (1 channel), UART (4 channels), I2C (1 channel), CAN (1 channel).
- Functional safety: software load reduced by Self-diagnostic and disconnection-detection assistance functions for the A/D converter, clock frequency accuracy measurement circuit, independent watchdog timer, RAM test assistance functions using the DOC and other circuits.
- Supply voltage: 5V. Independent power supplies can be used for the AFE block and microcontroller. Voltages of 1.8 to 5.5 V can be supported.
- Operating temperature: -40°C to +85°C, -40°C to +105°C
- Package: 48-pin QFP with 7 mm square. 40-pin QFP with 6 mm square.