Reusable porous metal filters 3D printed with ExOne technology were manufactured to fit inside a plastic respirator cartridge designed by the University of Pittsburgh. The combined units, now undergoing initial testing, could deliver sterilizable personal protection equipment for long-term use.
NORTH HUNTINGDON, Pa. — (BUSINESS WIRE) — April 27, 2020 — The ExOne Company (Nasdaq: XONE), the global leader in industrial 3D printers using binder jetting technology, and the University of Pittsburgh, a leading public research university based in Pittsburgh, have partnered to develop reusable metal filters that fit into a specially designed respirator cartridge for sustainable, long-term protection against contaminants, such as COVID-19.
This press release features multimedia. View the full release here: https://www.businesswire.com/news/home/20200427005107/en/
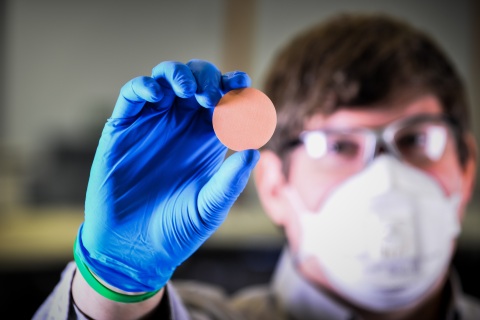
ExOne R&D Manager Kyle Myers, PhD, with a 3D printed porous copper filter, now in testing, that is reusable, sterilizable and sustainable, eliminating waste. The filter fits into a cartridge designed by Pitt, and it can be printed to fit a variety of medical needs. (Photo: Business Wire)
ExOne’s binder jetting technology is a high-speed form of 3D printing that can produce metal parts with specific porosity levels that can effectively filter out contaminants while allowing airflow.
ExOne has 3D printed respirator filters in two metals — copper and 316L stainless steel — and a range of porosity levels for use inside a unique cartridge designed by the Mechanical Engineering & Materials Science department in Pitt’s Swanson School of Engineering. Initial testing for airflow and filtration efficiency is currently underway, and the filters are being optimized with the goal of adhering to an N95 respirator standard.
“Our team has been working urgently to expedite this promising and reusable solution for medical personnel on the frontlines of fighting the COVID-19 pandemic,” said John Hartner, ExOne CEO. “Our customers routinely print porous metal filters for a variety of purposes, and we are confident that we’ll have a solution soon that can enable medical personnel to sterilize metal filters for repeated reuse, eliminating waste. Once approved, we can print these filters in a variety of sizes for respirators, ventilators, anesthesia masks or other equipment.”
“The advantage of binder jet 3D printing over other additive manufacturing methods for this filter application is the ability to utilize the porosity of the printed part and then fine tune it during the high temperature densification or sintering process to achieve optimum filtering and airflow performance,” said Markus Chmielus, Associate Professor of Mechanical Engineering and Materials Science at the Swanson School.
3D Printed Metal Filter Project Details
ExOne’s binder jetting technology uses an industrial printhead to selectively deposit a liquid binder onto a thin layer of powdered material, layer by layer, until a final object is formed. After 3D printing powdered metals, the object is then sintered in a furnace to dial in a specific level of porosity. While binder jetted metal is typically sintered to full density, some applications require a specific level of porosity, such as filters.
To test filters in different metals and porosities, Dr. Chmielus’ research group is using CT scanners to analyze the microstructure and porosity of the filters. Ansys, the global leader in engineering simulation, also based near Pittsburgh, is providing additional computer simulation support to analyze and optimize the performance of the filters.
While copper and stainless steel filters are currently being tested, copper has been known to have antibacterial properties since ancient times. The first recorded use of copper to kill germs was in the Edwin Smith Papyrus, the oldest known medical document in history, according to the Smithsonian. Many studies have proven copper’s disinfectant powers. One landmark 2015 study, funded by the Department of Defense, revealed that copper alloys contributed to a 58% reduction in infections. COVID-19 research also suggests the virus dies faster on copper than on other surfaces.
About ExOne
ExOne is the pioneer and global leader in binder jet 3D printing technology. Since 1995, we’ve been on a mission to deliver powerful 3D printers that solve the toughest problems and enable world-changing innovations. Our 3D printing systems quickly transform powder materials — including metals, ceramics, composites and sand — into precision parts, metalcasting molds and cores, and innovative tooling solutions. Industrial customers use our technology to save time and money, reduce waste, improve their manufacturing flexibility, and deliver designs and products that were once impossible. As home to the world’s leading team of binder jetting experts, ExOne also provides specialized 3D printing services, including on-demand production of mission-critical parts, as well as engineering and design consulting. Learn more about ExOne at www.exone.com or on Twitter at @ExOneCo. We invite you to join with us to #MakeMetalGreen™.
About the Swanson School of Engineering
The University of Pittsburgh’s Swanson School of Engineering is one of the oldest engineering programs in the U.S. and has excelled in basic and applied research during the past decade with focus areas in sustainability, energy systems, advanced manufacturing, bioengineering, micro- and nanosystems, computational modeling and advanced materials development. More than 180 faculty members serve more than 3,700 undergraduate, graduate and PhD students across six departments: bioengineering, chemical and petroleum engineering, civil and environmental engineering, electrical and computer engineering, industrial engineering, and mechanical engineering and materials science.
View source version on businesswire.com: https://www.businesswire.com/news/home/20200427005107/en/
Contact:
Media:
Sarah Webster
Global Marketing Director
724-516-2336
Email Contact