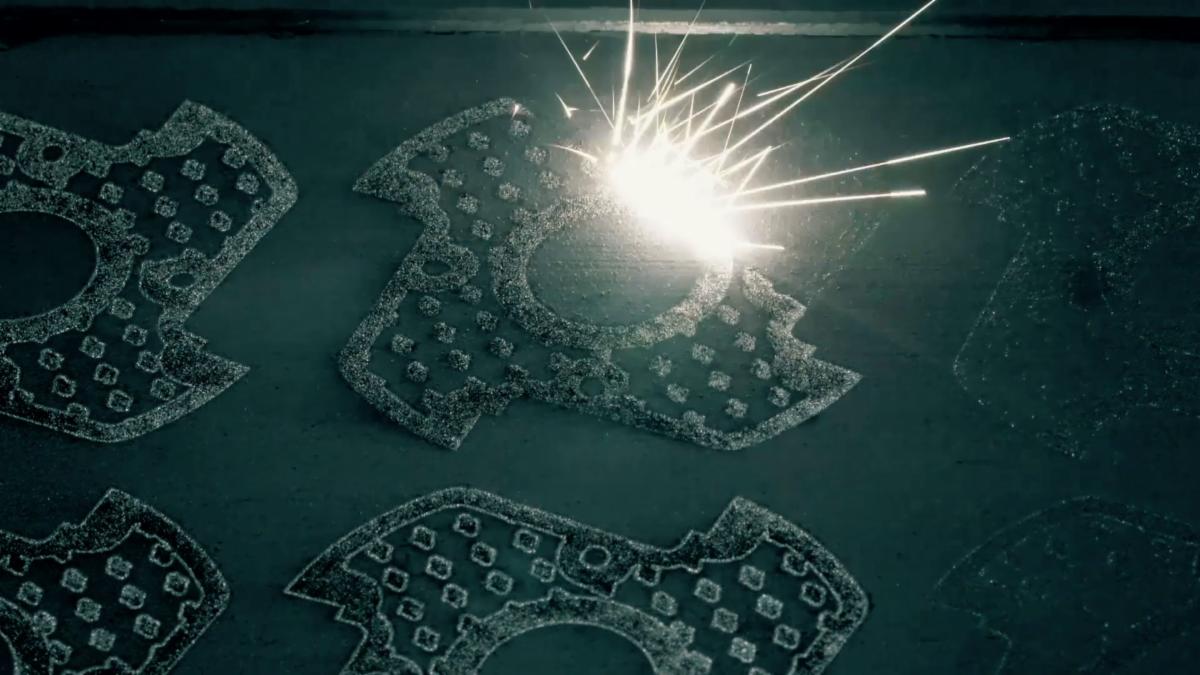 |
Additive manufacturing of parts looks set to upend the supply of components globally. A small-scale trial of 3D manufactured parts is helping Sandvik Mining and Rock Solutions and leading mining company Boliden explore the potential. |
Sweden has a long and noble history of mining, with evidence of human activity dating back to prehistoric times. But old does not mean primitive, as a trial of cutting-edge technology between Sandvik and Swedish mining and metals giant Boliden shows. Additive manufacturing – or 3D printing as it is more commonly known – is maturing fast, and has progressed from printing plastic components to now being able to print ceramics and metals. To discover the potential of the technology, Boliden has teamed up with Sandvik to run a trial that will see machine parts printed digitally and installed on underground drill rigs.
Proof-of-concept
The trial with Sandvik involves a set of specially redesigned components printed digitally at a Sandvik-managed facility in Italy, with their performance being monitored on machines in Boliden’s underground mine worksites - first in Sweden, then in Ireland. At least in theory, the 3D metal parts could perform as well – or even better – than traditionally manufactured items. The first components have just been put into operation in the Garpenberg mine, with performance still to be evaluated.
“Additive manufacturing shows a lot of potential, both in reducing carbon footprint within the supply chain, through reduced or eliminated need for transport and storage of parts and also shorter delivery times. This trial will give us a deeper understanding on how we can move forward and develop our business in a competitive way,” says Ronne Hamerslag, Head of Supply Management at Boliden.
Local manufacturing is ‘the future’
3D printing is an exciting prospect for OEMs too, as Sandvik’s Erik Lundén, President, Parts & Services at Sandvik Mining & Rock Solutions explains: “Mining equipment can last up to 25 years – and needs to be supported throughout that time – even in the most remote of locations. We have many different SKUs (stock keeping units), and from an inventory point of view we can’t tie up the capital that keeping all these parts in stock would entail. 3D printing of parts locally offers us the prospect of not only getting parts to the customer much faster, but doing so far more sustainably.”
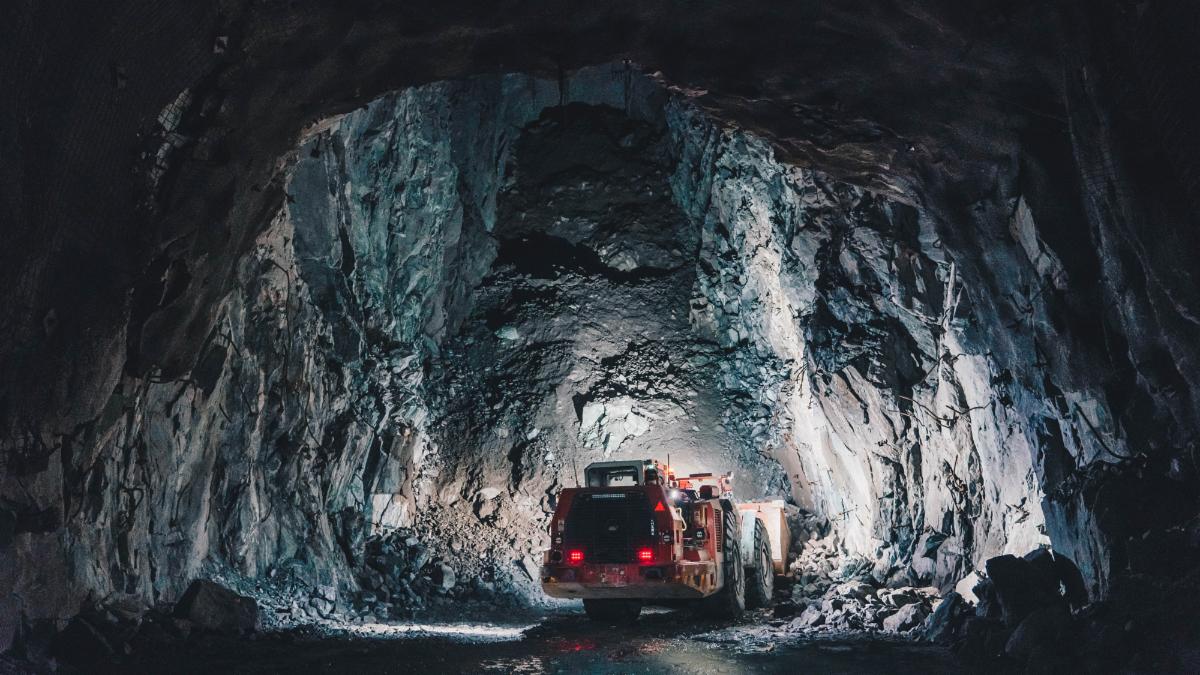 |
Although in theory any part could in future be 3D printed, it is likely to be maintenance and repair operating items that are the first to get the additive manufacturing treatment, such as the bushes, brackets, drill parts, etc. that customers need to change every 3,000-4,000 hours. But printing of the parts is only one part of the puzzle that the trial with Boliden is trying to solve. Another is working out the future business model for 3D printed parts. Who does the printing – the OEM, the miner, or a third-party printing company? What will the costs be? What about intellectual property rights, warranties and liabilities? All these things - and more - need to be resolved in the development of a 3D printed future.
Game changer for parts business
“If you ask me, it’s the most exciting thing that’s happening in the supply chain,” says Boliden’s Hamerslag. “Its efficiency, speed and climate friendliness mean that we have to investigate additive manufacturing closely. We are only at the proof-of-concept stage with Sandvik right now, but it’s already clear that it could become a game-changer for the spare parts business in mining – for both miners and equipment manufacturers.”
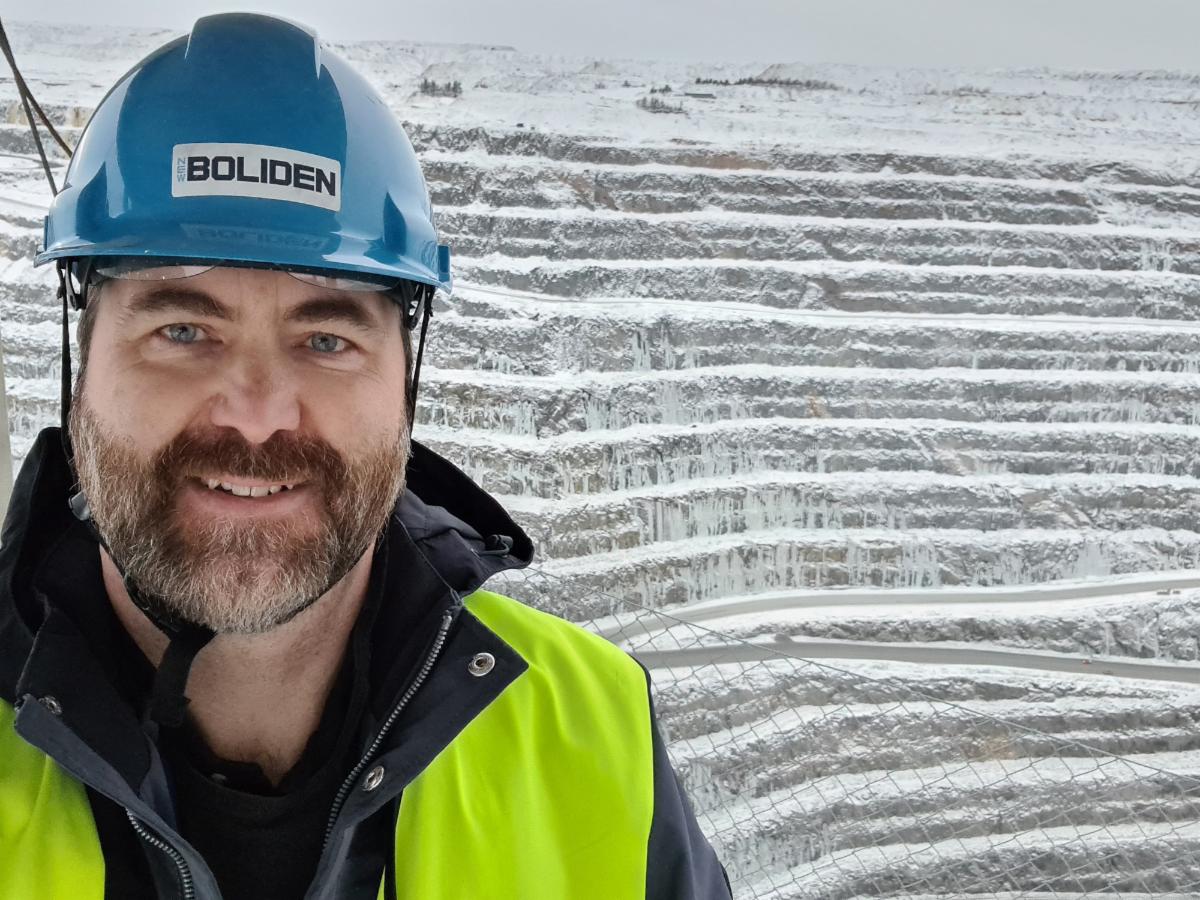 |
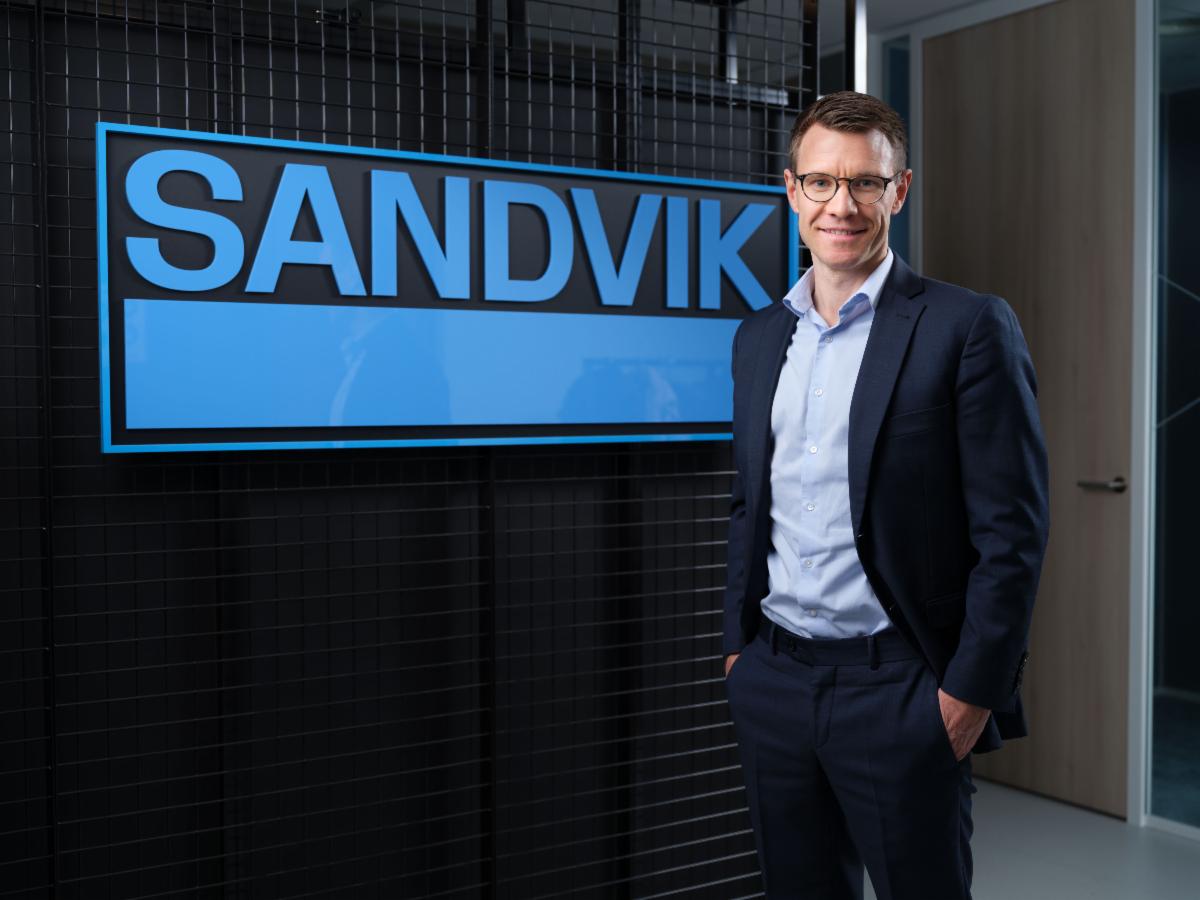 |
Figure 1. Ronne Hamerslag, Head of Supply Management at Boliden. |
Figure 2. Erik Lundén, President, Parts & Services at Sandvik Mining & Rock Solutions. |
Sandvik Group
Sandvik is a high-tech and global engineering group offering products and services that enhance customer productivity, profitability and safety. We hold world-leading positions in selected areas – tools and tooling systems for metal cutting; equipment and tools, service and technical solutions for the mining industry and rock excavation within the construction industry; products in advanced stainless steels and special alloys as well as products for industrial heating. In 2021, the Group had approximately 44,000 employees and revenues of about 99 billion SEK in about 150 countries.
Sandvik Mining and Rock Solutions
Sandvik Mining and Rock Solutions is a business area within the Sandvik Group and a global leading supplier of equipment and tools, parts, service, digital solutions and sustainability-driving technologies for the mining and construction industries. Application areas include rock drilling, rock cutting, loading and hauling, tunneling and quarrying. In 2021, sales were approximately 41.4 billion SEK with about 15,500 employees.
Krista Walsh
Sustainable Business, Marketing
& Communication Manager
Parts and Services
Sandvik Mining and Rock Solutions
+31 6219 38860
|
Brian O’Sullivan
Daredevil
+44 77 333 50307
|